3D printing, the process of layering various materials into objects, appears to be moving mainstream, with new applications, such as printing skin cells for burn patients, as the institute of regenerative medicine at Wake Forest University (NC) has been experimenting with.
Here’s a bit of background for those unfamiliar with the process: it consists of making a three dimensional object by creating successive layers of material, particularly plastic or metal, not unlike painting.
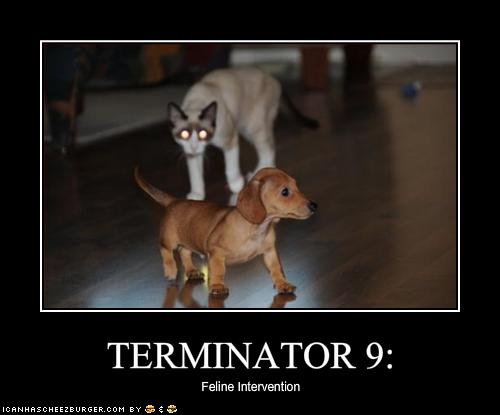
This technology has been in use for years, by designers to produce prototypes. Advances in technology are making 3D printing a more viable alternative to more “conventional” production methods used in economies of scale, particularly due to its versatility.
One of the more fascinating applications is bio-printing, the generation of tissue to reconstruct skin, as mentioned earlier, bone and organs. There remains work to be done, but early animal experimentation seems promising.
As to manufacturing, 3D printing makes more efficient use of material: while conventional casting of aircraft parts using titanium results in about 90% wasted metal, 3D printing instead uses powdered titanium which the printer then fuses with laser or electron beam. Unused powder can be used to make more parts as needed.
The technology also redefines “prêt-a-porter” (made to wear) by for instance printing shoes which exactly follow the contours of the foot.
While the technology and its applications will still take time to reach consumers more widely, it is becoming more affordable, with commercial printers starting around $30K, and personal units about half of that. Some companies will produce items on order for about 8 times the actual manufacturing cost.
Still, it should be possible to see even automobiles made to order, from an existing template, instead of huge lots filled with unsold units… And imagine what confectioners and chocolatiers could achieve..!